Steam Heat Radiators
The association had tried several times to have a pattern made for
casting new GW style steam heat radiators but with little success. This
time around, with work being done by the SVR's own team of pattern
makers and using different techniques, we have, at last, achieved
success despite initially getting off "wrong footed" by originally
making the fins from polyester gel-coat.
Notes: Brian Oldford, Bridgnorth Pattern Shop. Photos: Colin Jenkins and Brian Oldford. |
The continuing saga of the trials and tribulations of keeping our customer's feet warm!
The small 39 fin radiator have cast well and once fettled will be fine. But the first 85 fin radiator wasn't a success because the core flexed/floated more than expected despite being secured with chaplets. This was a combination of the need to pour the iron hot (to flow into all the fins of such a long rad) and the use of chaplets that were a little too light.
The foundry remoulded it and recast it with the core supported with heavier chaplets. These proved to be heavy enough to prevent the core flexing/floating but light enough to fuse fully into the molten iron.
Chaplets are small pieces of a similar material that is being cast (iron in this case) that are sometimes included within the mould to support cores. The idea is they will remain firm enough during the pour to prevent the core floating/flexing yet get hot enough to completely fuse with the molten metal and thus produce a homogenous casting. Barr and Grosvenor make their own, cast on the premises, thus ensuring a similar mix.
The use of a segmented pattern has proved a success. The moulder was very pleased with the release of all those fins from the air-set sand and we will now cast a total of 14 short and 2 long radiators.
|
|
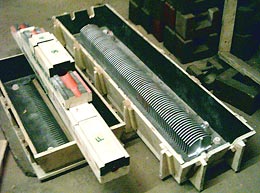
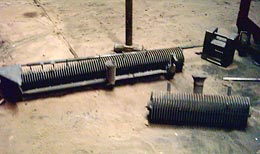
Two photographs taken at Barr & Grosvenor's foundry after they recast the long radiator successfully, along with some of the moulding equipment. The feeds and vents (sprues) will be removed when the castings are fettled. |
With the patterns now complete (5-3-06) we have been in touch with Barr & Grosvenor, the Wolverhampton foundry frequently used by the SVR for loco parts, to quote for the initial requirement of 2 long and 10 small radiators. We will then take the equipment to the foundry and guide the moulder through the use of it to mould the first few.
|
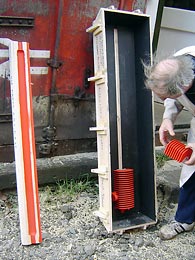 This image shows the finned segments being assembled into the moulding box for the large (85 fin) radiator. The segment with the steam inlet can be seen in place already. When the box is being prepared for the other mould-half the section with the steam inlet will be reversed to point to the right. Part of the core-box to produce the cavity within the radiator can be seen to the left of the moulding box.
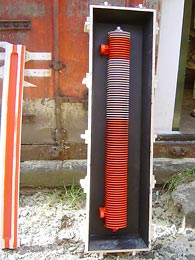
This view shows the all the pattern segments assembled for a large radiator. (The photographer arrived before the pattern-maker had finished painting.)
|
|
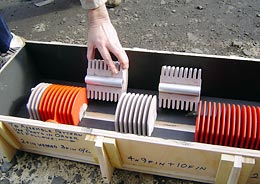
This view shows how the pattern segments locate into a semi-circular groove along the floor of the moulding box. Shorter moulding boxes and shorter cores enable the medium and short length radiators to be produced. At the time these captions were written the painting of all the parts has been completed. The only outstanding work is to drill and tap 1/4" Whit the 1" dia. aluminium 'backbone' to permit the moulder to remove the mould sections from the sand. See the casting of the Dean style buffers for details.
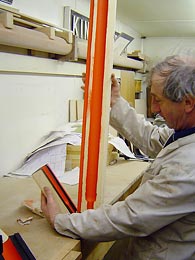
This view shows how the 'lid' of the core-box
is made in sections to permit the moulder the get a good fill of sand
within the cavity.
Photos: Colin Jenkins. Notes: Brian Oldford |
The original plan was to cast aluminium patterns from a polyester resin
master (as shewn* in the photographs below). This was abandoned for a
number of reasons. It was found that to cure completely the original
cast polyester resin fins needed to be left in the mould for up to seven
days, thus taking far too much time with the limited number of fin
moulds available. The radiator for the guard's compartment has 85 fins.
Additionally, even on the completed smallest radiator (39 fins) it was
found the very large surface area and thin section between fins led to
some foundry sand jamming between the fins unless the draft on the fins
was controlled very accurately. Remarkably, modern foundry sand binder
technology is far less forgiving to any dimensional inaccuracy that
occurs in the pattern. It was also decided that there would need to be
an significant amount of hand work dressing the surface imperfections of
the finished aluminium patterns before they could be used productively.
After further discussions it was agreed that a new pattern would be made
in segments of no more than ten fins to ease removal of the finned
sections from the air-set sand. The new pattern has now being made,
being turned on a lathe from solid pre-cast foamed polyester. This
material, albeit expensive, is adequately strong but has the real
benefit of being extremely stable thus minimising the dimensional
inaccuracy problem.
|
|
The patternmaker also discovered another advantage to making a segmental pattern. By careful selection of the number of fins on each section it will be possible for the moulder to select from the kit of parts to assemble any one of the 3 different length radiators found in GW coaches.
For simplicity the pattern maker made different coreboxes for each length radiator, these were quite straightforward to make as the cores are a simple cylindrical section, reduced in diameter at the ends for the core-prints.
To bring the construction right up to date: The mind
numbingly repetitive job of turning the 85 half-fin
segments has now been completed (no CNC machines
here!). The web detail has been added to the end fins
and the steam inlet and condensate outlet added.
Moulding boxes for smallest (39 fins), medium sized (57
fins) and largest (85 fins) radiators are complete. The
only outstanding items are the 3 core boxes. These will
be made using half round cutters in a 1850w router. All being well they should be finished about mid March.
*GWR spelling!
|
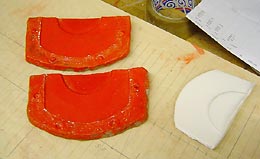
The fins for the pattern are cast in epoxy resin using the red fibre glass moulds. The pattern maker can only cast two per night so this is a long process. Photos by Colin Jenkins. |
|
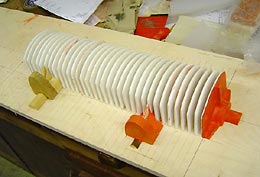
Here the fins are being assembled to produce the final pattern. From this we will cast an aluminium pattern, as the fins are rather too delicate to keep long term. Afterwards the pattern maker will carry on adding more fins for the next size heater. |